SnapTrak Series: Resolver and Screw Terminal Industrial I/O Backplane Mount Snaptrack
Features:
- Low Cost-No Expensive Chassis or Connectors
- No Soldering-All Connections are provided by durable industrial grade terminal blocks.
- Electronics snap in and out without disturbing adjacent hardware.
- Entire Encoder system can be installed in just a few minutes with only a screwdriver.
- Factory repairable encapsulated electronics provide added resistance to dust, dirt, moisture, vibration & shock.
- Zener Diodes-User Accessible for over voltage protection
- Because every connection is clearly identified and easy to reach, SNAPTRAK Encoders are easier to install, wire and maintain.
Description:
Computer Conversions Snaptrak Encoders are versatile, low cost, easy to use and highly reliable encoders that convert any rotary shaft input into absolute and/or incremental data corresponding directly to shaft angle displacement. Binary, BCD, Analog and quadrature square wave outputs are available to assure direct compatibility with a variety of industrial controls.
Absolute resolutions up to 10,000 parts/turn BCD, and 65, 536 parts/turn binary are offered with a selection of universally adaptable interface formats to assure a synchronous stable, and secure data input to any programmable controller, computer, or microprocessor buss available. Open collector and three-state outputs are optional for long data transmission and buss compatability.
Absolute BCD versions may be provided with any scale factor desired to correspond with direct inches, meters, degrees, or percentage.
Incremental resolutions from 256 to 16,384 pulses per revolution are available with A & B quadrature square wave pulse trans, zero marker pulse and a full set of compliments for reliable rate monitoring, step and repeat positioning, and digital tachometer feedback functions.
The basic system consists of an electromagnetic transducer (resolver) and an easy to use Snaptrak decoder.
Since the shaft angle pickoff is a highly reliable resolver, the Snaptrak system is free from deficiencies such as limited life brushes, or lamps, brush noise, ambiguities, and limited resolution usually associated with conventional mechanical, magnetic or optical encoder type systems. In addition, the Snaptrak decoder provides the highest system electrical noise immunity attainable, coupled with the ability to operate over long and simple cable runs. Transducer cables only require six conductors, shielding is optional, and the system is capable of maintaining 1000' cable runs in severe RFI environments.
No soldering, crimping, or lugs required. The Snaptrak decoder features industrial grade high barrier terminal blocks for all inputs and outputs; captive wire clamps are provided to accept 12-30 Awg. direct wire inputs. All terminations are permanently screened for visual identification, and the entire system can be installed in just a few minutes with only a screwdriver.
Additional electronics are not required because the resolver excitation generator, isolation circuitry, data conversion and interface logic are all provided in a single trouble free (factory repairable), snap-on encapsulated assembly. The encapsulated electronics provides added resistance to shock, vibration, dust, and moisture, making it suitable for many harsh industrial and mobile applications.
Because the entire conversion process is ratiometric and referenced to its self-generated AC supplies, inexpensive commercial grade DC power supplies (regulated to +/-10%), are sufficient to attain full rated accuracy. Single +12 or +15VDC power inputs are optional for use with existing supplies. Zener diodes provide over voltage and transient protection, and are user accessible for field replacement.
The Snaptrak employs a high speed, nonambiguous type, two servo loop to insure that the output data is always fresh, continuously available and accurate to the maximum input rate. A DC velocity output is available for speed regulation, and a count up/down signal may be provided for direction indication or used for turns counting applications.
A built-in test bit (Bite) can be made available, acknowledging the encoders tracking mode to detect malfunction of the encoder system or a no motion condition on its associated drive.
The Snaptrak Encoder's high speed tracking abilitty, velocity output, scaleability, and modular construction, in addition to its simplicity of interfacing, make it ideally suited for all shaft angle digitizing applications with the O.E.M. in mind. Snaptrak decoders may be provided for compatibility with existing resolvers or synchros, if so desired.
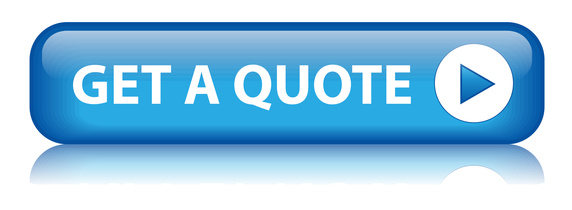