SDT RDT Series - Multispeed Synchro and Multispeed Resolver to Digital, Industry Standard Size modules Isolated Reference and Signal Input Options
Features:
- Accuracy: to +/-20 arc.Seconds.
- Auto-corrects to +/-90 degree (fine) misalignments.
- BIT with field miss-alignment fault detect.
- No false 180 degree nulls.
- All Ratios: 8:1, 10:1, 16:1, 32:1, 36:1, 128:1.
- Insensitive to Variations in Frequency & Amplitude
- High Tracking Rate: 1000 degree/s (Coarse).
- Encapsulated for Safety, Reliability, Shock /Vibration
- Wide Band 47-3000 Hz. Reference Frequency.
- Commercial, Industrial and Military Temp. Models
- Non-Ambiguous, Pre-combined, Binary Scaled Linear 16 Bit Output.
- Choice of Transformer Isolated Inputs, or Low Cost Solid State Input Models.
- Low Power, and +/-12 DC Models, (Ideal for Mobile Applications).
- Transformer Isolated Models provide added Protection from Lightning (No path to Ground), Field potentials, and Electrical Noise.
Description:
The SDT/RDT Series, are single module, tracking, Multi-speed synchro/resolver to digital converters designed for Military and Industrial Applications. They will accept Electrical Multi-speed, or Geared (dual speed) Multi-turn; Synchro or Resolver input sets (Fine/ Coarse), having the most standard ratio’s, and convert them into a single non-ambiguous 16 Bit data word with up to +/-20 arc. seconds accuracy.
A “BIT” Built-in-Test output is also available. No external modules are required and either solid state or transformer type Scott T inputs are provided intenally in a 2.6”x3.1”x.8”H package. Angular input rates of up to 1000/ sec. can be tracked with no accuracy degradation and a voltage output proportional to velocity may be obtained.
Data is continuously available, accurate and always fresh up to the maximum input rate.These units are insensitive to signal and reference amplitude variations due to the basic ratiometric conversion technique used. Power required is +15 and +5VDC on the units. Accuracy applies over the operating temperature range.
The SDT Series’ are available with either low cost, solid state inputs, or having internal transformer isolated inputs.
The availability of Internally Transformer Isolated Models offers guaranteed trouble free operation in the most extreme application and environments. Transformer Isolation provides added safety, system integrity and security; with respect to service personnel, user circuitry, and power supplies (Isolated from the high voltage and inductive field potentials). The Isolation eliminates concerns with respect to ground-loops, ground interjected (intermittent and ghostly) field noise, inductive surges, differing potentials, and high voltage field transients from effecting the typically sensitive user circuitry, associated power supplies, and other device or system sharing the power, reference sources, or signal lines. In Radar and Antenna applications, Transformer Isolated models have proven themselves to save whole system electronics consoles from being damaged by lightning otherwise, because the field lines lack any continuity or path to ground. All internal transformers are manufactured to MIL-T-27 and are designed to withstand high-pot to 500VDC minimum.
The user need not be a Synchro/Resolver expert to design his system; no external components, or added transformers or modules are required, these value added converters provide a single part solution for ease of use, rapid integration, long term reliability and field proven assurance.
Timing and Interface:
The output data changes respective of realized displacement on the input angle and in proportion to speed. The output data is monotonic, whereby the every 1 least significant bit of change is realized on the output with no missing counts. A 1-2 microsecond “Converter Busy” (C/B) pulse is generated the instant the data output is being incremented/ decremented, and stabilized within 0.2 microseconds respective of the C/B’s leading edge. Interface considerations range from monitoring the C/B, to using the “Inhibit” (INH) signal input to stall the converter. A low level inhibit occurring during a C/B will be ignored until the new data is set on the outputs. To use the INH, simply: clear to zero, wait 2.0 Usec., read or transfer the data. Because applying the INH stalls the conversion process, always release the INH after reading or transferring data.
Safety and Construct:
All modules are encapsulated in an inert polymer that is self-extinguishing, flame retardant to U.L. 94VO, and will not feed or combust. Printed Circuit card material is flame retardant FR4, assemblies are conformal-coated for moisture resistance. Transformers are manufactured to MIL-T-27 and capable of withstanding high-pot to 500VDC. Case is flame resistant glass filled Diallyl Phthalate per MIL-M-14. Because all the high voltage circuitry is encapsulated within the self-extinguishing and flame retardant potting material; added protection is provided with respect to the potential for component failure, shock and vibration, and are suitable for the most severe industrial and military applications.
Functional Operation:
In a typical 1 x 36 application: The heart of the multispeed converter is two solid state control transformers (SCT’s) driving a type two servo loop. A typical SCT provides an output representing the sine of the error between the input angle and current output position, whereby the phase polarity represents the direction +/-, and the amplitude represents the magnitude over a limited range. The SCT output is demodulated and conditioned to drive a voltage controlled oscillator that increments/decrements a counter driving the outputs and fed back into the SCT. The counter feedback reduces the error in the SCT to close the loop.
The resulting tightly follows the analog inputs to dynamically track input deviations real-time and without any lag (except for a minimal that may be experienced with extreme accelerations on the input). Gross error resulting from a step input would cause the loop to null on the coarse SCT to within approximately 2.5 degrees, whereby the loop then nulls onto the fine SCT to yield optimum precision. A stick-off ; voltage and a small SCT offset is introduced into the loop, to prevent any false 180 degree nulls.
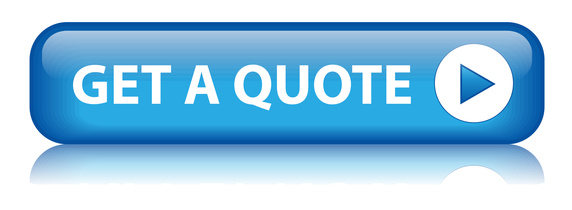