DC SnapTrack Series: Resolver and Screw Terminal Backplane Mount Track with Analog Outputs
Features:
- Brushless-Rotary System
- Angle to VDC or 4-20 ma.
- Velocity/Tachometer outputs
- Single +24VDC Power Input
- Up to 1000' Cable Runs
- Ultra High Noise Immunity
- Ratiometric Tracking Conversion
- No Adjustments Required
- DC Outputs Short Circuit Protected
- 5 Millivolts Maximum Ripple
- Crisp-Dynamic Response
- Anti-Deadband Feature
Description:
Designed for industrial applications where position data may be conveniently utilized for input to chart recorders, X-Y plotters , DPM's, Servo, Process, or Programmable Controls, and Analog Computer input ports.
The Snaptrack DC Series are an analog output variation of Computer Conversion Corporation's standard Snaptrack Encoders.
This Series includes a ratiometric rotary transformer based transducer as the feedback element, and a convenient screw-terminal styled remote decoder.
The Snaptrack DC models use an internal, solid state type II servo loop to actually track the rotary shaft input, continuously converting it to a precise (real time) linear DC voltage (or 4-20 ma. current) corresponding directly to the input shaft position.
The internal type II servo-loop provides both of the benefits of a dynamic lag free response (higher speeds) with a crisp and ultra-stable output approaching, or at zero speed input.
Because the decoder naturally maintains a maximum 5 millivolt ripple (on the DC output); filtering is neither employed or required, providing continuous clean and jitter-free output suitable for use in many variable speed applications.
Since the shaft angle pick-off is a highly reliable resolver; the Snaptrack system is free from deficiencies such as limited life brushes, or lamps, brush noise, ambiguities, and limited resolution usually associated with conventional mechanical, magnetic or optical encoders. In addition, the Snaptrack decoder provides the highest electrical noised immunity attainable, coupled with the ability to operate over long and simple cable runs. Transducer ables only require six conductor, shielding is optional, and they system is capable of maintaining 1000’ cable runs in severe RFI environments.
The ratiometric conversion allows the transducer to operate over -20 to +125 C temperatures with no degradation of output.
The DC Snaptracks have an anti-deadband feature that prevents any true discontinuity of the output over zero crossings. A minimum .012% (typical) hysterisis is applied to the decoders internal servo loop; to insure a jitter-free response and finite definition of both 0 and 359.9 angles.
A linear DC velocity output is available for speed regulation, and high accuracy linear DC velocity outputs are optioned for use as tachometer feedback and/or speed synchronizing applications.
Differential units are offered for many shaft synchronizing, or in-synch measurement applications. Differential DC Snaptracks include two transducers as inputs, and one decoder to provide a single DC or current loop output proportionate to a 0 to 360, or +180 absolute difference between shaft inputs.
A simple two-wire terminal change distinguishes clockwise verse counter clockwise rotation for an increasing output.
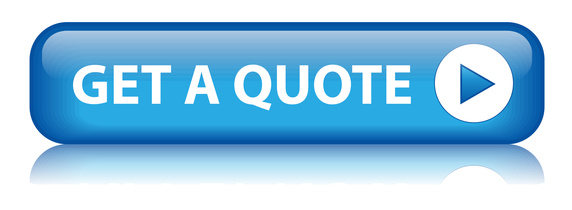